United Nations Video: UN Deputy Chief – CSW69 – For ALL Women and Girls: Beijing+30 | United Nations
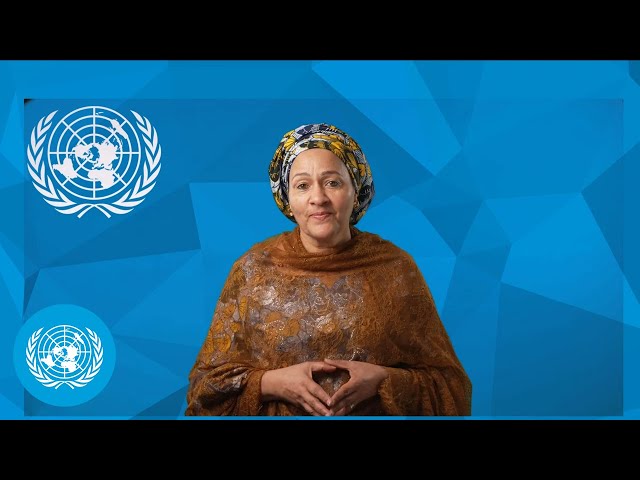
Amina J. Mohammed, Deputy Secretary-General's video message on the occasion of the 69th session of the Commission on the Status of Women (CSW69) UN Women-organized Side Event “For ALL Women and Girls: The Beijing+30 Action Agenda”, 12 March 2025.
Published: 16th Mar 2025 03:00:00 By: United NationsUnited Nations Video: Theo James, UNHCR Goodwill Ambassador | #ActNow | United Nations
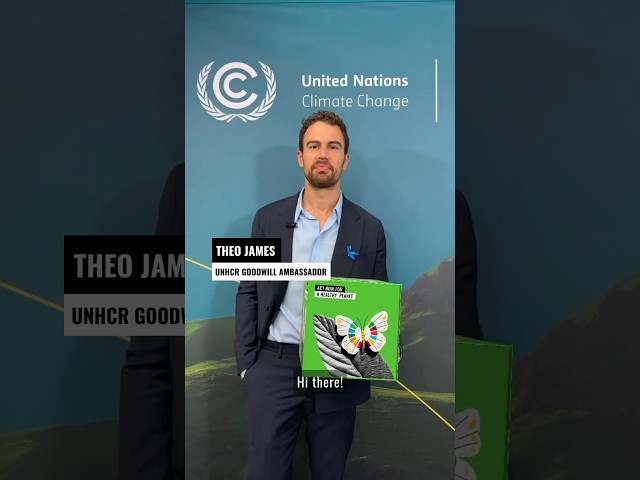
While at the UN Climate Change Conference COP29 in Baku, UNHCR Goodwill Ambassador Theo James discussed how the climate crisis is driving displacement and making life harder for those who have already been uprooted. He urged everyone to #ActNow for a better future for all.
Learn more and start seeing the difference your actions can make: https://www.un.org/actnow
Published: 16th Mar 2025 01:00:51 By: United NationsUnited Nations Video: The Story of Us: Art Across the African Diaspora | United Nations

The Stories of Us sculpture exhibition features five large-scale “talking drums” that were envisioned and painted by artists across the African diaspora. They focus on the theme of resistance, spanning Afro-descendant communities’ roots, to emancipation, to the tradition of “good trouble.” The exhibition serves as an invitation to reimagine who we want to be, and to act in the spirit of unity. It runs at United Nations Headquarters from early March to the end of April 2025, bookended by the International Day of Remembrance of the Victims of Slavery and the Transatlantic Slave Trade (25 March) and the Permanent Forum for People of African Descent (14-17 April).
Published: 16th Mar 2025 09:00:28 By: United NationsUnited Nations Video: UN Secretary-General Affirms Solidarity with Bangladesh and Rohingya Refugees | United Nations
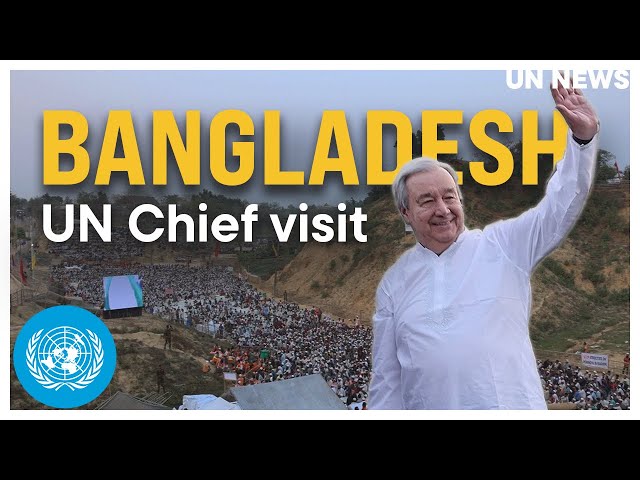
During his visit to Bangladesh, UN Secretary-General António Guterres underscored the “pivotal moment” the country is facing as it navigates a period of significant transition and reform. Mr. Guterres met with the Chief Adviser of the government, Muhammad Yunus in Dhaka, and other leaders.
The Secretary-General’s visit, coinciding with the holy month of Ramadan, was an opportunity to express solidarity with both the Bangladeshi people and the Rohingya refugees who have found shelter in the country. Mr. Guterres visited the refugee camps in southern Cox’s Bazar, meeting with Rohingya refugees and participating in an Iftar meal with them and members of the host community in the evening.
During his visit to the Rohingya refugee camps in southern Bangladesh, Mr. Guterres vowed to do everything in his power to prevent further hardship as drastic aid cuts threaten food supplies and other critical relief efforts.
The UN Chief assures the people of Bangladesh that the United Nations stands ready to assist the country in fostering peace, national dialogue, trust and healing during this pivotal moment of political transition.
Published: 16th Mar 2025 02:00:16 By: United NationsUnited Nations Video: UN Secretary-General in solidarity with refugees in Bangladesh and beyond
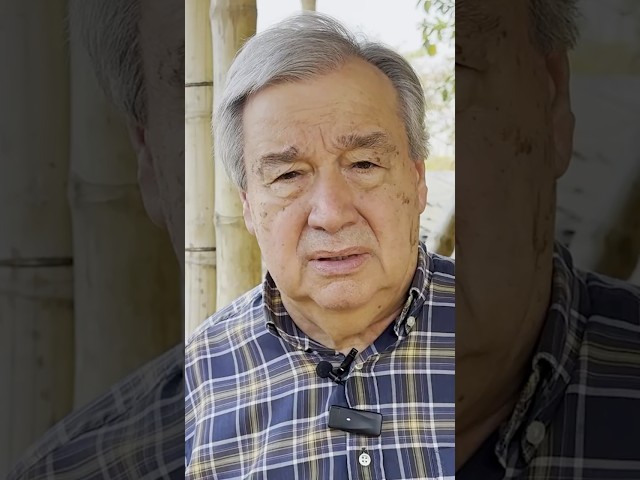
Visiting Cox’s Bazar in Bangladesh, United Nations Secretary-General António Guterres says “the entire refugee population depends on humanitarian aid.
Until the conflict and the systematic persecution they have fled ends, we must support them.
The international community has an obligation to invest - now - in aid for people who have suffered so much.”
Published: 15th Mar 2025 06:28:20 By: United Nations
CNN Video: Trump envoy on his meeting with Putin

US special envoy to the Middle East Steve Witkoff tells CNN’s Jake Tapper about his “positive” meeting with Russian President Vladimir Putin. #CNN #News
Published: 16th Mar 2025 05:27:35 By: CNNCNN Video: Fareed’s Take: Trump administration's 'war on colleges'

CNN’s Fareed Zakaria details how moves by President Donald Trump’s administration are impacting higher education in the United States. #CNN #News
Published: 16th Mar 2025 05:00:47 By: CNNCNN Video: Trump orders strikes on Houthi rebels in Yemen
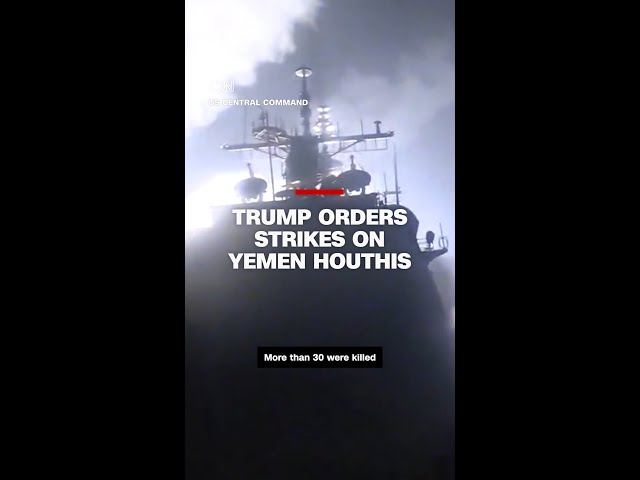
More than 30 were killed and over 100 injured after US President Donald Trump ordered “decisive” military action against Houthi rebels in Yemen. The Iran-backed military group has regularly targeted shipping lanes in the Red Sea, hampering global trade. #cnn #news #yemen #trump
Published: 16th Mar 2025 04:53:20 By: CNNCNN Video: Roy Wood Jr. and panel react to Trump's handling of US economy and tariffs on Canada and Mexico

Roy Wood Jr. hosts "Have I Got News For You," a smart and edgy take on the news of the week. This week, sports journalist Bomani Jones and comedian and writer Nimesh Patel joined the panel. Watch the full episodes on CNN.com https://www.cnn.com/videos/title-2506994
#hignfy #CNN
Published: 16th Mar 2025 04:14:23 By: CNNCNN Video: How Trump has redecorated the Oval Office
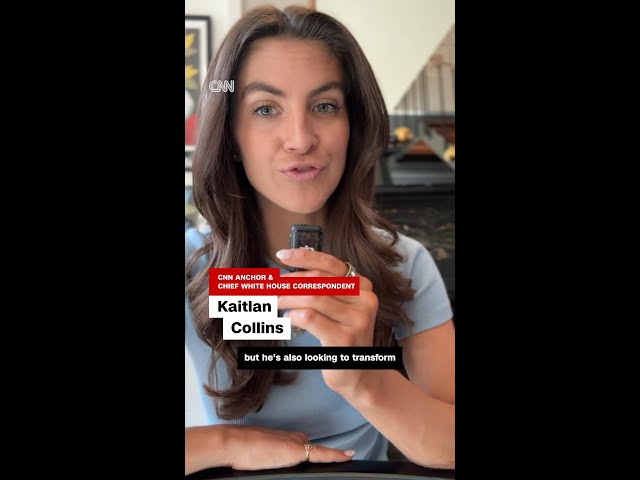
CNN’s Chief White House correspondent Kaitlan Collins looks at how President Donald Trump redecorates the White House and his plans for the future. #cnn #news #politics
Published: 16th Mar 2025 03:15:35 By: CNN
BBC News Video: Tornadoes tear through southern US leaving dozens dead | BBC News
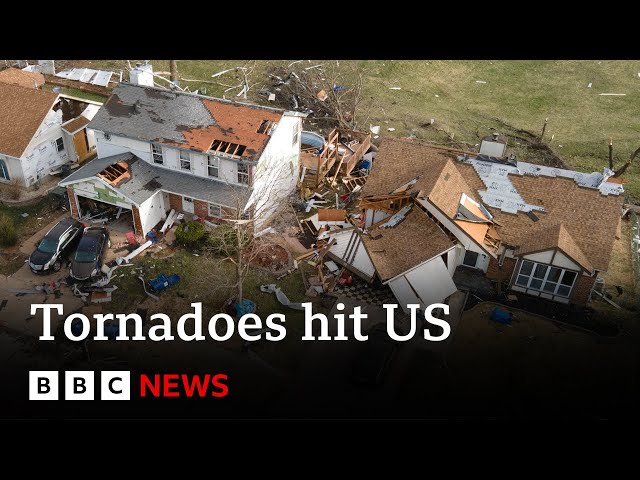
At least 34 people have died in the US - including 12 in Missouri alone - after deadly tornadoes tore through several south-eastern states, flipping cars and flattening homes.
In Kansas, at least eight people died after more than 55 vehicles were involved in a crash due to a dust storm.
More than 250,000 properties were without power across seven states - including Michigan, Missouri and Illinois - overnight into Sunday, according to tracker PowerOutage.
Further severe weather is expected for the region, with tornado watches issued.
Subscribe here: http://bit.ly/1rbfUog
For more news, analysis and features visit: www.bbc.com/news
#US #Weather #BBCNews
Published: 16th Mar 2025 02:00:04 By: BBC NewsBBC News Video: Six deaths were reported after the deadly tornado in Mississippi. #Tornado #Mississippi #BBCNews
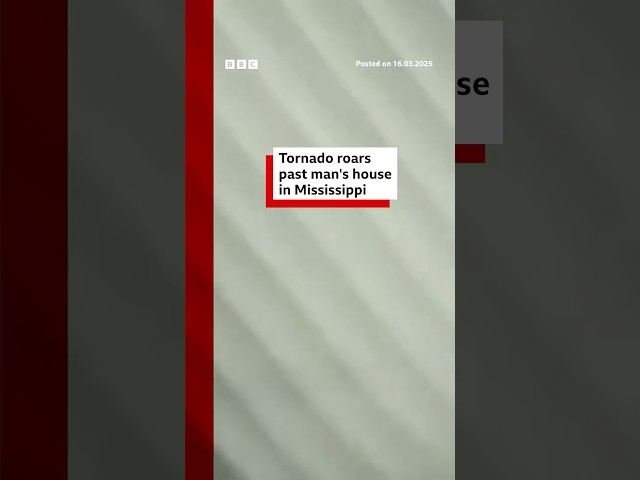
Subscribe here: http://bit.ly/1rbfUog
For more news, analysis and features visit: www.bbc.com/news
#BBCNews
Published: 16th Mar 2025 12:04:49 By: BBC NewsBBC News Video: US launches wave of air strikes on Yemen's Houthis | BBC News

The US has launched a "decisive and powerful" wave of air strikes on Houthi rebels in Yemen, President Donald Trump has said.
He cited the armed group's attacks on shipping in the Red Sea as the reason behind the US move.
The Houthi-run health ministry said at least 31 people were killed and 101 others were injured in the strikes.
The group - which began targeting shipping in response to the Israel-Hamas war in Gaza - said its forces would respond to US strikes.
Subscribe here: http://bit.ly/1rbfUog
For more news, analysis and features visit: www.bbc.com/news
#US #Yemen #BBCNews
Published: 16th Mar 2025 12:01:21 By: BBC NewsBBC News Video: Nasa astronauts hug 'great' new crew after being stranded for nine months. #Nasa #BBCNews
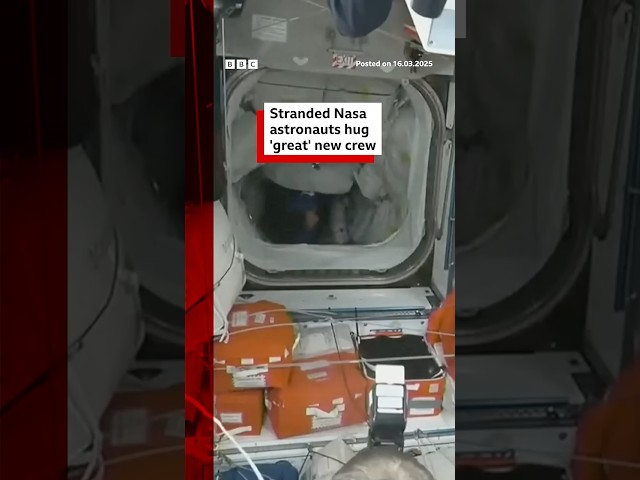
Subscribe here: http://bit.ly/1rbfUog
For more news, analysis and features visit: www.bbc.com/news
#BBCNews
Published: 16th Mar 2025 11:00:38 By: BBC NewsBBC News Video: Nightclub fire in North Macedonia leaves at least 51 dead | BBC News
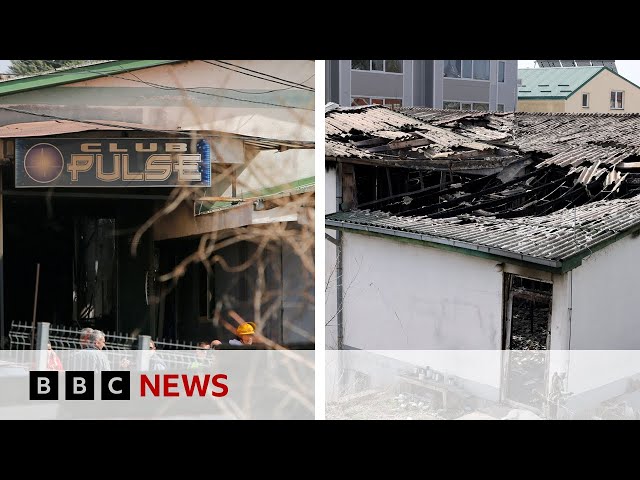
At least 51 people have been killed and more than 100 injured in a nightclub fire in North Macedonia, officials said.
The blaze is said to have started around 02:30 (01:30 GMT) at the Pulse club in Kocani, a town around 100 km (60 miles) east of the capital, Skopje.
Footage posted on social media shows the building engulfed in flames.
As many as 1,500 were said to have been attending a concert by the band DNK, a hip-hop duo popular in the country.
Subscribe here: http://bit.ly/1rbfUog
For more news, analysis and features visit: www.bbc.com/news
#Fire #NorthMacedonia #BBCNews
Published: 16th Mar 2025 10:26:10 By: BBC News
ODN Video: LIVE: Scene in North Macedonia After Deadly Nightclub Fire
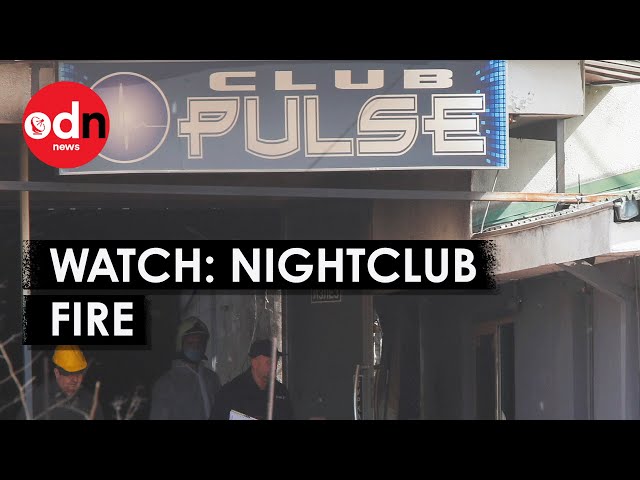
At the scene in North Macedonia after a fatal nightclub fire killed at least 51 people.
#ukraine #russia #keirstarmer
Subscribe here: http://bit.ly/ODNsubs
TikTok: https://www.tiktok.com/@ondemandnews
Twitter: https://twitter.com/ODN
Facebook: https://www.facebook.com/ODN/
If you wish to purchase any of our clips for commercial use, please visit: http://www.itnproductions.co.uk/news/
Published: 16th Mar 2025 12:44:14 By: On Demand NewsODN Video: Horrifying Nightclub Fire in North Macedonia Kills Dozens
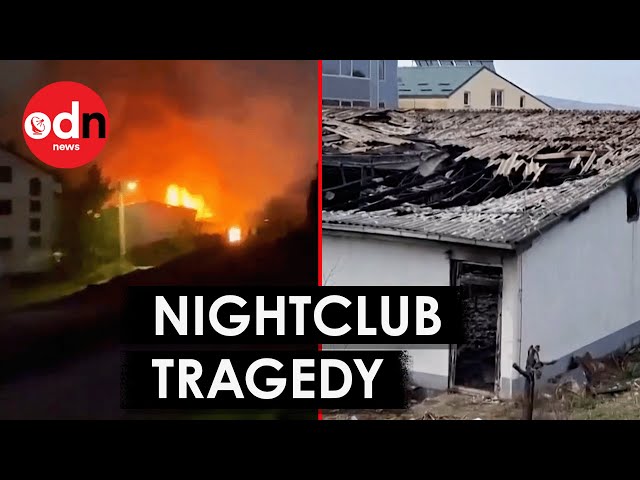
Footage posted on social media shows a packed nightclub in Kocani, North Macedonia, engulfed in fire.
A devastating fire overnight in a nightclub in Kocani, North Macedonia, has killed at least 51 people.
More than 155 people were also injured in the tragedy, officials said.
The fire started at around 02:30 local time at Pulse club during a concert by the band DNK.
Interior Minister Pance Toshkovski said pyrotechnics, mainly fireworks, set off inside the building caused the roof to catch fire.
He also revealed that arrest warrants have been issued for four people.
#macedonia #nightclub #fire
Subscribe here: http://bit.ly/ODNsubs
TikTok: https://www.tiktok.com/@ondemandnews
Twitter: https://twitter.com/ODN
Facebook: https://www.facebook.com/ODN/
If you wish to purchase any of our clips for commercial use, please visit: http://www.itnproductions.co.uk/news/
Published: 16th Mar 2025 12:38:15 By: On Demand NewsODN Video: New Eyewitness Footage Captures Devastation in Kursk Region
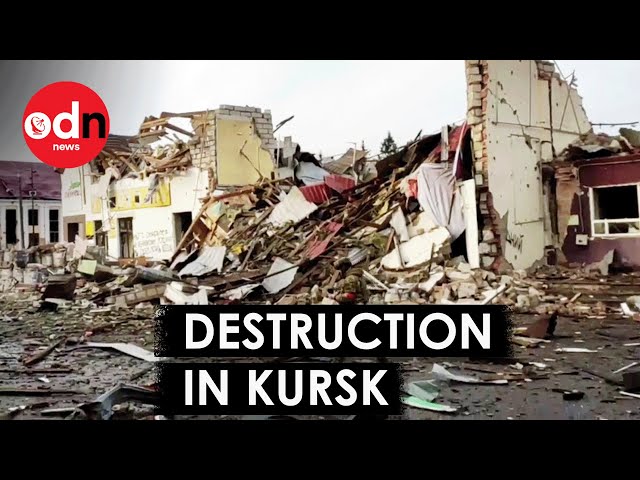
The Russian military has released new footage showing a key town in the Kursk border it claims to have retaken from Ukraine.
Sudzha, which was once populated with around 5,000 people, is now almost completely destroyed.
It was the biggest town seized by Kyiv’s forces last August as part of an unexpected cross-border offensive.
Earlier this week the Kremlin said that Russian soldiers had surrounded Ukrainian troops in the region.
But President Volodymyr Zelenskyy denied these claims during a virtual meeting hosted by UK Prime Minister Keir Starmer.
#ukraine #russia #kursk
Subscribe here: http://bit.ly/ODNsubs
TikTok: https://www.tiktok.com/@ondemandnews
Twitter: https://twitter.com/ODN
Facebook: https://www.facebook.com/ODN/
If you wish to purchase any of our clips for commercial use, please visit: http://www.itnproductions.co.uk/news/
Published: 15th Mar 2025 06:20:33 By: On Demand NewsODN Video: Philippines’ Rodrigo Duterte Appears at ICC Court After Dramatic Arrest

This was the moment former Philippine president Rodrigo Duterte appeared at the International Criminal Court (ICC) by a video link, days after his arrest in Manila.
Duterte attended court on Friday over alleged crimes against humanity related to his illegal drug crackdowns.
The 79-year-old had been allowed to appear at The Hague online due to his long flight and existing health issues.
In a message filmed on his flight to the Netherlands, the former president pledged to “continue to serve” his country.
Subscribe here: http://bit.ly/ODNsubs
TikTok: https://www.tiktok.com/@ondemandnews
Twitter: https://twitter.com/ODN
Facebook: https://www.facebook.com/ODN/
If you wish to purchase any of our clips for commercial use, please visit: http://www.itnproductions.co.uk/news/
Published: 15th Mar 2025 01:42:38 By: On Demand NewsODN Video: LIVE: Starmer Addresses Nation After Crucial Meeting With Leaders About Ukraine
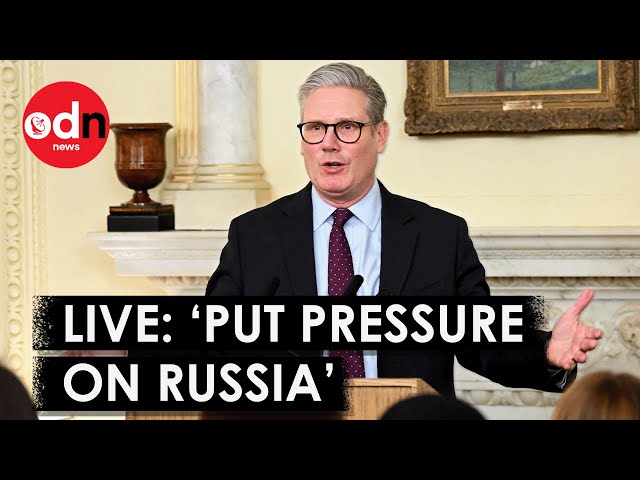
UK Prime Minister Keir Starmer holds a news conference following his virtual meeting with several world leaders willing to help support a ceasefire in Ukraine.
#ukraine #russia #keirstarmer
Subscribe here: http://bit.ly/ODNsubs
TikTok: https://www.tiktok.com/@ondemandnews
Twitter: https://twitter.com/ODN
Facebook: https://www.facebook.com/ODN/
If you wish to purchase any of our clips for commercial use, please visit: http://www.itnproductions.co.uk/news/
Published: 15th Mar 2025 12:49:19 By: On Demand News
CBC Video: Mark Carney to visit France, U.K in 1st foreign trip as PM

Just days after being sworn into office, Prime Minister Mark Carney will embark on his first trip abroad in the new job. Carney's office says he'll travel to Paris, then to London where he's expected to meet with King Charles only weeks after his predecessor, Justin Trudeau, held his own meeting with the monarch.
Read more: https://www.cbc.ca/1.7484873
»»» Subscribe to CBC News to watch more videos: http://bit.ly/1RreYWS
Connect with CBC News Online:
For breaking news, video, audio and in-depth coverage: http://bit.ly/1Z0m6iX
Follow CBC News on TikTok: https://bit.ly/3TnHioe
Follow CBC News on Twitter: http://bit.ly/1sA5P9H
Find CBC News on Facebook: http://bit.ly/1WjG36m
Follow CBC News on Instagram: http://bit.ly/1Z0iE7O
Subscribe to CBC News on Snapchat: https://bit.ly/3leaWsr
Download the CBC News app for iOS: http://apple.co/25mpsUz
Download the CBC News app for Android: http://bit.ly/1XxuozZ
»»»»»»»»»»»»»»»»»»
For more than 80 years, CBC News has been the source Canadians turn to, to keep them informed about their communities, their country and their world. Through regional and national programming on multiple platforms, including CBC Television, CBC News Network, CBC Radio, CBCNews.ca, mobile and on-demand, CBC News and its internationally recognized team of award-winning journalists deliver the breaking stories, the issues, the analyses and the personalities that matter to Canadians.
Published: 16th Mar 2025 06:06:40 By: CBC NewsCBC Video: As Trump pauses Columbia River Treaty, is Canada’s water at risk?
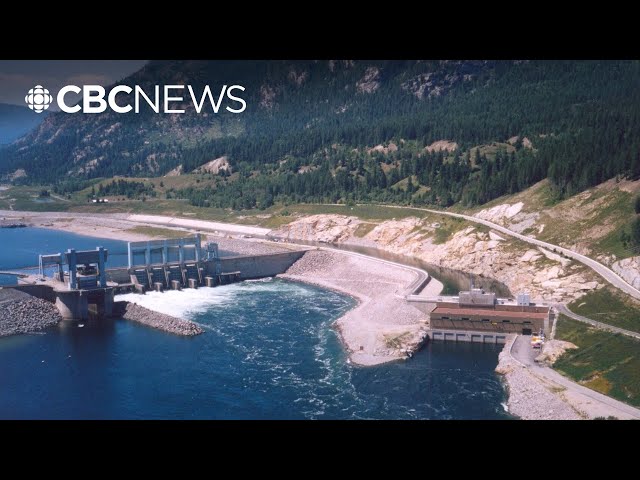
As the U.S. has paused negotiations with Canada over the wide-reaching Columbia River Treaty, which regulates everything from flood control to water supply, one academic says Canada is 'ill-prepared' to deal with threats that could come from U.S. ownership of its water.
Read more: https://www.cbc.ca/1.7480986
»»» Subscribe to CBC News to watch more videos: http://bit.ly/1RreYWS
Connect with CBC News Online:
For breaking news, video, audio and in-depth coverage: http://bit.ly/1Z0m6iX
Follow CBC News on TikTok: https://bit.ly/3TnHioe
Follow CBC News on Twitter: http://bit.ly/1sA5P9H
Find CBC News on Facebook: http://bit.ly/1WjG36m
Follow CBC News on Instagram: http://bit.ly/1Z0iE7O
Subscribe to CBC News on Snapchat: https://bit.ly/3leaWsr
Download the CBC News app for iOS: http://apple.co/25mpsUz
Download the CBC News app for Android: http://bit.ly/1XxuozZ
»»»»»»»»»»»»»»»»»»
For more than 80 years, CBC News has been the source Canadians turn to, to keep them informed about their communities, their country and their world. Through regional and national programming on multiple platforms, including CBC Television, CBC News Network, CBC Radio, CBCNews.ca, mobile and on-demand, CBC News and its internationally recognized team of award-winning journalists deliver the breaking stories, the issues, the analyses and the personalities that matter to Canadians.
Published: 16th Mar 2025 05:46:41 By: CBC NewsCBC Video: Carney government is on ‘war-time footing,’ says industry minister

Chief political correspondent Rosemary Barton speaks with Minister of Innovation, Science and Industry Anita Anand about Prime Minister Mark Carney’s new cabinet and her new portfolio. Plus, The Sunday Scrum discusses what this means for an expected upcoming election.
»»» Subscribe to CBC News to watch more videos: http://bit.ly/1RreYWS
Connect with CBC News Online:
For breaking news, video, audio and in-depth coverage: http://bit.ly/1Z0m6iX
Follow CBC News on TikTok: https://bit.ly/3TnHioe
Follow CBC News on Twitter: http://bit.ly/1sA5P9H
Find CBC News on Facebook: http://bit.ly/1WjG36m
Follow CBC News on Instagram: http://bit.ly/1Z0iE7O
Subscribe to CBC News on Snapchat: https://bit.ly/3leaWsr
Download the CBC News app for iOS: http://apple.co/25mpsUz
Download the CBC News app for Android: http://bit.ly/1XxuozZ
»»»»»»»»»»»»»»»»»»
For more than 80 years, CBC News has been the source Canadians turn to, to keep them informed about their communities, their country and their world. Through regional and national programming on multiple platforms, including CBC Television, CBC News Network, CBC Radio, CBCNews.ca, mobile and on-demand, CBC News and its internationally recognized team of award-winning journalists deliver the breaking stories, the issues, the analyses and the personalities that matter to Canadians.
Published: 16th Mar 2025 05:44:29 By: CBC NewsCBC Video: A behind-the-scenes look at Canada-U.S. trade negotiations in Washington
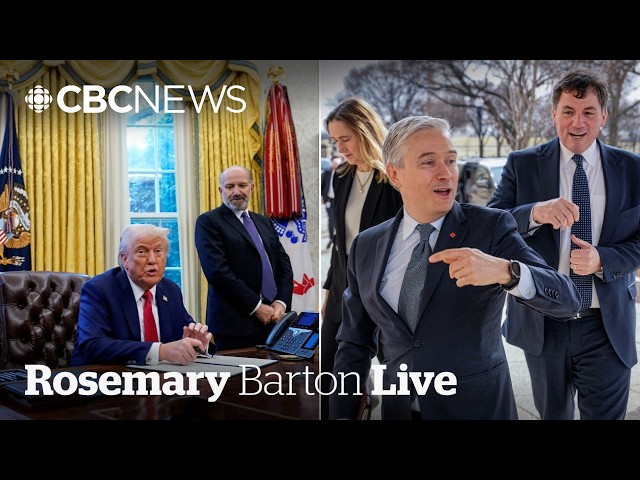
Chief political correspondent Rosemary Barton speaks with Ambassador Kirsten Hillman about Canada’s ongoing trade negotiations in Washington ahead of further tariffs from the Trump administration.
»»» Subscribe to CBC News to watch more videos: http://bit.ly/1RreYWS
Connect with CBC News Online:
For breaking news, video, audio and in-depth coverage: http://bit.ly/1Z0m6iX
Follow CBC News on TikTok: https://bit.ly/3TnHioe
Follow CBC News on Twitter: http://bit.ly/1sA5P9H
Find CBC News on Facebook: http://bit.ly/1WjG36m
Follow CBC News on Instagram: http://bit.ly/1Z0iE7O
Subscribe to CBC News on Snapchat: https://bit.ly/3leaWsr
Download the CBC News app for iOS: http://apple.co/25mpsUz
Download the CBC News app for Android: http://bit.ly/1XxuozZ
»»»»»»»»»»»»»»»»»»
For more than 80 years, CBC News has been the source Canadians turn to, to keep them informed about their communities, their country and their world. Through regional and national programming on multiple platforms, including CBC Television, CBC News Network, CBC Radio, CBCNews.ca, mobile and on-demand, CBC News and its internationally recognized team of award-winning journalists deliver the breaking stories, the issues, the analyses and the personalities that matter to Canadians.
Published: 16th Mar 2025 05:03:50 By: CBC NewsCBC Video: Trump is ‘blowing things up to put them back together’: former U.S. ambassador to EU
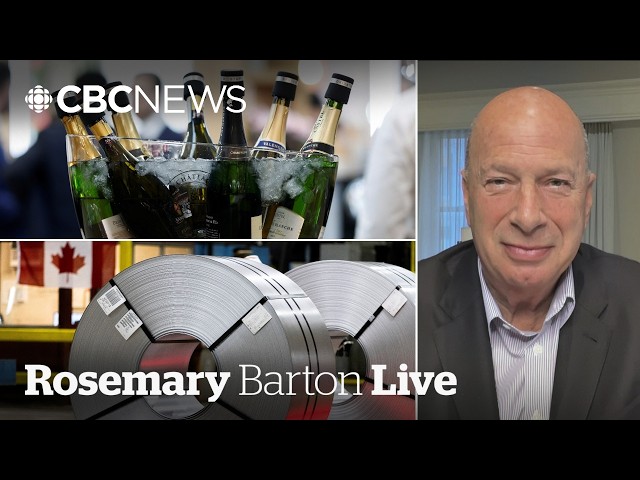
Chief political correspondent Rosemary Barton speaks with U.S. President Donald Trump’s former ambassador to the European Union, Gordon Sondland, about Trump’s goals with tariffs on Canada and the EU.
»»» Subscribe to CBC News to watch more videos: http://bit.ly/1RreYWS
Connect with CBC News Online:
For breaking news, video, audio and in-depth coverage: http://bit.ly/1Z0m6iX
Follow CBC News on TikTok: https://bit.ly/3TnHioe
Follow CBC News on Twitter: http://bit.ly/1sA5P9H
Find CBC News on Facebook: http://bit.ly/1WjG36m
Follow CBC News on Instagram: http://bit.ly/1Z0iE7O
Subscribe to CBC News on Snapchat: https://bit.ly/3leaWsr
Download the CBC News app for iOS: http://apple.co/25mpsUz
Download the CBC News app for Android: http://bit.ly/1XxuozZ
»»»»»»»»»»»»»»»»»»
For more than 80 years, CBC News has been the source Canadians turn to, to keep them informed about their communities, their country and their world. Through regional and national programming on multiple platforms, including CBC Television, CBC News Network, CBC Radio, CBCNews.ca, mobile and on-demand, CBC News and its internationally recognized team of award-winning journalists deliver the breaking stories, the issues, the analyses and the personalities that matter to Canadians.
Published: 16th Mar 2025 04:59:57 By: CBC News
International Video: Mark Carney sworn in as new Canadian prime minister

Mark Carney has been sworn in as the new Canadian prime minister at a ceremony in Ottawa.
[Subscribe: https://bit.ly/C4_News_Subscribe]
The former Bank of England governor has replaced Justin Trudeau as the leader of the Liberal Party after being voted in by party members last weekend.
-------
Get more news at our site - https://www.channel4.com/news/
Follow us:
TikTok - https://www.tiktok.com/@c4news
Instagram - https://www.instagram.com/channel4news/
Twitter - https://twitter.com/Channel4News
Facebook - https://www.facebook.com/Channel4News/
Published: 14th Mar 2025 05:24:02 By: Channel 4 NewsInternational Video: Hamas says it will release US-Israeli hostage

Hamas says it has agreed to release Edan Alexander, a 21-year-old American-Israeli hostage - along with the bodies of four dual US nationals - if Israel begins the second phase of ceasefire talks.
[Subscribe: https://bit.ly/C4_News_Subscribe]
Israel described it as 'psychological warfare'.
-------
Get more news at our site - https://www.channel4.com/news/
Follow us:
TikTok - https://www.tiktok.com/@c4news
Instagram - https://www.instagram.com/channel4news/
Twitter - https://twitter.com/Channel4News
Facebook - https://www.facebook.com/Channel4News/
Published: 14th Mar 2025 05:23:11 By: Channel 4 NewsInternational Video: Duterte at ICC in the Hague

The former Philippines president Rodrigo Duterte has appeared via video link at the International Criminal Court in The Hague.
[Subscribe: https://bit.ly/C4_News_Subscribe]
Duterte faces charges of crimes against humanity linked to the deadly 'war on drugs ' which he oversaw during his time in power.
-------
Get more news at our site - https://www.channel4.com/news/
Follow us:
TikTok - https://www.tiktok.com/@c4news
Instagram - https://www.instagram.com/channel4news/
Twitter - https://twitter.com/Channel4News
Facebook - https://www.facebook.com/Channel4News/
Published: 14th Mar 2025 05:22:10 By: Channel 4 NewsInternational Video: American Airlines jet catches fire
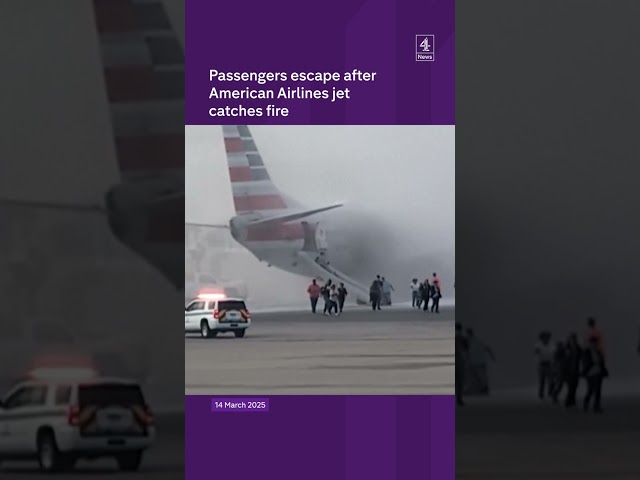
178 passengers and crew managed to escape from an American Airlines jet which caught fire after an engine fault.
[Subscribe: https://bit.ly/C4_News_Subscribe]
The Boeing 737-800 was on its way to Dallas Fort Worth - but diverted to Denver after the crew reported 'engine vibrations'. 12 people were treated for minor injuries.
-------
Get more news at our site - https://www.channel4.com/news/
Follow us:
TikTok - https://www.tiktok.com/@c4news
Instagram - https://www.instagram.com/channel4news/
Twitter - https://twitter.com/Channel4News
Facebook - https://www.facebook.com/Channel4News/
Published: 14th Mar 2025 01:39:01 By: Channel 4 NewsInternational Video: Voters at town hall angry at Trump policies
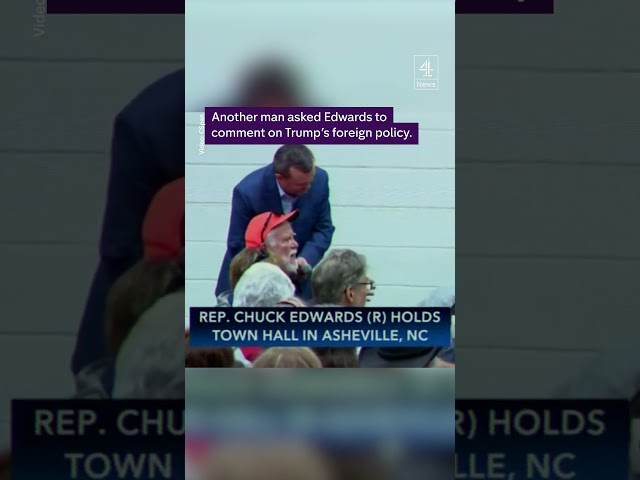
A town hall meeting in Asheville, North Carolina turned rowdy when attendees started heckling Republican Chuck Edwards about Trump's policies on government spending, annexing Greenland and Canada, plus his approach to Ukraine.
[Subscribe: https://bit.ly/C4_News_Subscribe]
-------
Get more news at our site - https://www.channel4.com/news/
Follow us:
TikTok - https://www.tiktok.com/@c4news
Instagram - https://www.instagram.com/channel4news/
Twitter - https://twitter.com/Channel4News
Facebook - https://www.facebook.com/Channel4News/
Published: 14th Mar 2025 01:11:16 By: Channel 4 News